MAG Ultrasonic Generator
Our modular ultrasonic components are designed for integration into production plants and meet the requirements to rise to the conceptual challenges of Industry 4.0. Straightforward mechanical and electrical integration into all systems for industrial production and comprehensive quality and process monitoring are equally important priorities. The high-speed ultrasonic generators can be controlled via fieldbus modules from all fieldbus systems (both those that are on general commercial sale and sector-specific solutions), resulting in cost savings and reduced wiring overheads. MAG generators are available rated at 0.6/1.2/2.4/3.6/4.8 and 7.2kW.
Advantages
at a glance
- Maximum cycle rates through dynamic control
- Constant power and amplitude across the entire voltage range from 180 V to 260 V
- High process repeat accuracy
- Proven state-of-the-art fieldbus interfaces
- Space-saving design optimized for 300mm deep switch cabinet
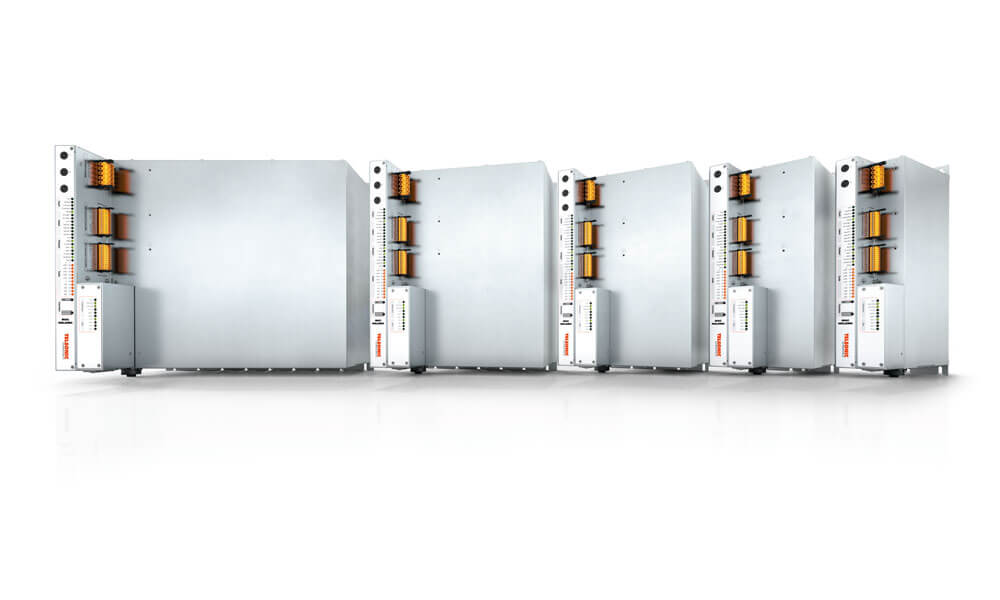

Torsional Ultrasonic Welding: SONIQTWIST®
Ultrasonic torsional welding supports automotive trends in the exterior and interior sectors such as weight reduction and thin wall materials with no read through on the A surface. On most thermal plastic materials, a higher weld strength is observed for torsional ultrasonic welding versus linear ultrasonic welding. Torsional welding SONIQTWIST® from Telsonic Ultrasonics complements the industry trends in lightweight construction as new thin wall thermal plastics and thin films are introduced into the industry to accomplish weight reduction and reduction in material costs. Torsional welding can weld wall thicknesses of 2.5mm and thinner. Telsonic’s gentle torsional welding process has been successful worldwide for decades. Some current relevant applications utilizing ultrasonic torsional welding are PDC, SLA, air handling systems, side skirts, and windscreen cleaning system.
Advantages
at a glance
- Suitable for plastics and metal welding
- Good accessibility, also in confined situations
- No membrane effect
- Gentle, low-vibration process (e.g. for sensors)
- For round and rectangular parts
TelsoFlex Software Control
Telsoflex offers a new experience on machine controls. With industry 4.0 standards, it offers various welding and splicing modes such as time, energy, power, and distance. The full range of functions in the Telso®Flex control software is used in both ultrasonic welding systems and automation lines. The software’s modular design meets the desire for customization and simultaneously future-proofs it for plastic welding, cut-and-seal, and metal welding applications.
The innovative visualization both reduces the complexity of operation and allows efficiency-enhancing functions to be adjusted intuitively. A powerful and high-resolution 12″ touch panel is a key element of the software control. It includes an individual brightness adjustment function and has the advantage of being usable while wearing gloves.
Advantages
at a glance
- Extendable and future-proof: Modular and customizable software architecture for ultrasonic welding systems (welding presses) and automation lines in plastic welding, as well as cut-and-seal and metal welding applications
- Innovative visualization: Clear, ergonomic, and intuitive user interface for easy operation in conjunction with a new resistive 12″ touch panel
- Industry 4.0 “Smart Factory Ready”: OPC UA secures the network connection between welding systems/automation lines and workstations outside of the production area